
The AconityMIDI is Aconity3D’s approach for a flexible production system. Equipped with an optional second process chamber, this system allows for parallelizing setup times while the main system is still producing. Additionally, process monitoring or high-temperature preheating of up to 1200 °C is also available for this system.
The AconityMIDI is also available as a DUAL-Laser system for further maximized productivity.
Additionally, the AconityMIDI may be equipped with the unique Vacuum option and Micro-LPBF configuration.
The passivation of the filter ensures fluent 3D printing and decreases operational expenses. Recycling of the powder can be optionally performed by AconitySIEVE – an automatic sieving station utilizing inert gas to prevent material degradation.

Technical Specification
Ø 100 mm x H 200 mm (optional reduction)
Ø 55 mm x H 200 mm (optional reduction)
QCW Single Mode Green 200 W / 500 W
F-Theta / 80 μm
3D Scan unit / 80 – 500 μm
3D Scan unit Green 535 nm / approx. 50 – 250 μm
Coaxial high speed CMOS
Camera for inline process view
Thermo camera for lateral process monitoring in IR spectrum
800 °C / Ø 100 mm x H 150 mm
1200 °C / Ø 70 mm x H 150 mm
Argon 4.6 / 6 bar
Nitrogen / 6 bar
Vacuum / < 2 mbar
< 5 l/min during process
< 30 l/min during purging
0 – 5 l/min for vacuum
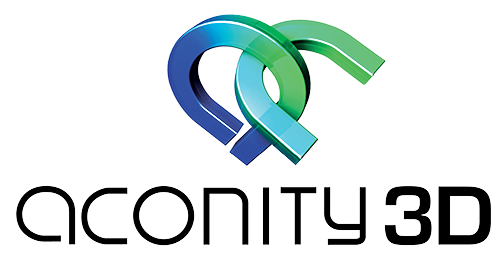
Worth noticing – ACONITY INLINE PROCESS MONITORING – Aconity3D is one of the leading providers of in-process monitoring systems for laser-based 3D printing of metals (LPBF). The process monitoring tool allows for inline identification of the influence of changed process parameters on the to-be-built part.
The featured video shows a comparison of the size of the melt pool for contour scans of two consecutively scanned layers.
Accordingly, the influence of changed laser processing parameters on the size of the melt pool may be identified. The featured video is part of Aconity3D’s ongoing effort towards increasing process understanding in the field of Laser Powder Bed Fusion (LPBF) with the ultimate goal of qualifying AM of metals for series applications. This is a very suitable feature for R&D activities focusing on these topics.